How OEE transforms Manufacturing Efficiency?
October 5, 2023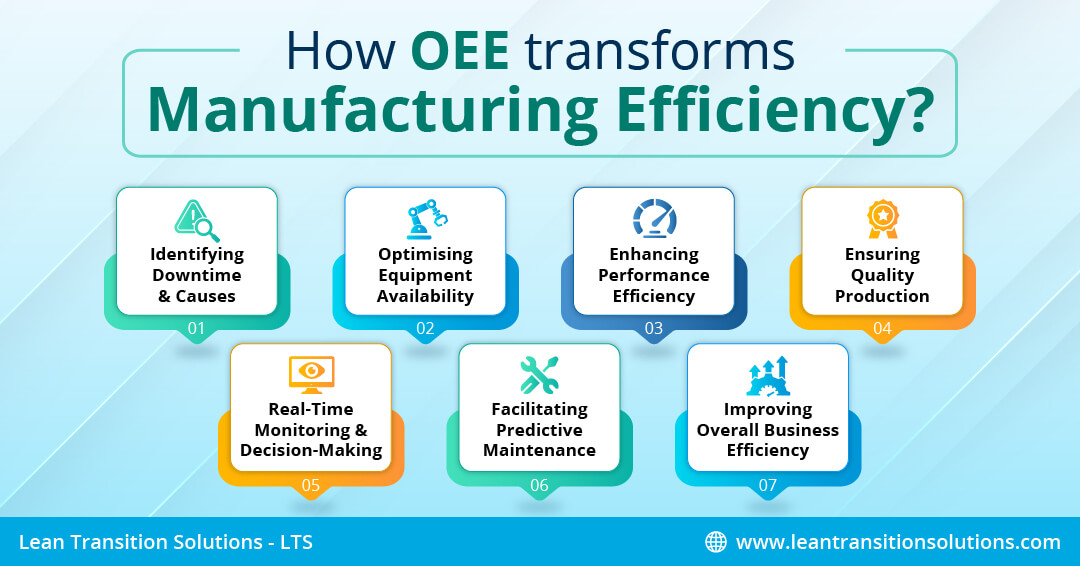
Efficient manufacturing is the ultimate goal for any organisation involved in production processes. Manufacturing efficiency directly impacts operational costs, product quality, customer satisfaction, and overall competitiveness in the market. Efficient manufacturing processes lead to timely delivery, minimised waste, and maximum resource utilisation for increased profitability and growth. However, optimising efficiency can be difficult when there are bottlenecks and obstacles within the production floor. So, it is necessary to identify performance issues and take prompt action.
OEE helps manufacturers analyse how effectively each manufacturing equipment is utilised. OEE dives deep into the heart of operations, analysing availability, performance, and quality, providing a holistic view of operational efficiency within the shop floor. This blog post explains how OEE transforms manufacturing efficiency, turning challenges into opportunities and inefficiencies into streamlined, high-performing operations.
Productivity vs Manufacturing Efficiency
Productivity and manufacturing efficiency are two important aspects of operational performance that are closely related but distinct from one another. Productivity refers to the output generated for each input unit, usually measured per labour hour or revenue per employee. It primarily focuses on the volume of goods produced or services delivered. On the other hand, manufacturing efficiency is all about optimising processes, reducing waste, and improving the utilisation of resources. It involves minimising downtime, increasing production speed, and ensuring high-quality output. While productivity measures the quantity of output, manufacturing efficiency emphasises the effectiveness and quality of that output. By tracking productivity and manufacturing efficiency, businesses can strike a balance to ensure high output levels, streamlined, cost-effective processes, superior products, customer satisfaction, and sustainable growth.
OEE - The key to Manufacturing Efficiency
Manufacturing industries rely on a critical metric called Overall Equipment Effectiveness (OEE) to evaluate the performance, availability, and quality of their equipment and production processes. By measuring the percentage of actual productive time compared to planned production time, valuable insights into manufacturing efficiency can be gained. OEE takes into account three important factors. By analysing these OEE factors, manufacturers can identify inefficiencies, pinpoint bottlenecks, and implement targeted improvements to enhance Overall Operational Efficiency (OOE). OEE factors include:
- Availability: It measures the actual operating time of equipment against the planned production time. It accounts for downtime, such as equipment breakdowns, changeovers, and other unplanned maintenance between production processes.
- Performance: Performance evaluates how well the equipment performs concerning its maximum speed or rate. It considers factors like slow cycles and minor stoppages that hinder optimal performance.
- Quality: Quality assesses the number of good units produced compared to the total units produced, considering defects, errors, or rework.
Common Challenges that affect your Manufacturing Efficiency
- Downtime and Equipment Failures: Manufacturing efficiency is hindered by frequent equipment breakdowns or downtime, leading to production delays and increased costs. Implementing preventive maintenance strategies and utilising predictive maintenance technologies can minimise such disruptions.
- Inefficient Production Processes: Outdated or poorly designed production processes can result in bottlenecks, wasted resources, and longer cycle times. Employing Lean Manufacturing techniques and process optimisation methodologies can streamline operations and improve Overall Operational Efficiency (OOE).
- Lack of Real-time Monitoring: With real time data analysis, manufacturers may be able to identify and address issues promptly. Utilising Industrial IoT (IIoT) devices and advanced analytics software for shop floor data collection enables real time monitoring, allowing immediate problem detection and resolution.
- Inadequate Workforce Training: Insufficient training can lead to errors, decreased productivity, and increased waste. Providing comprehensive training programs for employees ensures they possess the necessary skills to operate machinery efficiently and adhere to best practices.
- Supply Chain Disruptions: Unforeseen events can disrupt the supply chain, causing delays in raw material availability. Establishing robust supplier relationships, diversifying suppliers, and implementing risk mitigation strategies are vital in mitigating these challenges.
- Quality Control Issues: Poor quality products can lead to rework, waste, and customer dissatisfaction, impacting overall efficiency. Implementing strict quality control measures, utilising Six Sigma principles, and investing in advanced inspection technologies can enhance product quality and reduce defects.
- Energy Inefficiency: High energy consumption increases operational costs and contributes to environmental concerns. Implementing energy-efficient technologies and conducting energy audits can reduce energy consumption and promote environmental sustainability in manufacturing processes.
- Data Security Concerns: In the digital transformation era, safeguarding sensitive manufacturing data from cyber threats is really important. Implementing reliable data collection software can protect your valuable information and maintain the integrity of manufacturing operations.
How does OEE transform your Manufacturing Efficiency?
To improve manufacturing efficiency, it is crucial to clearly understand how Overall Equipment Effectiveness (OEE) works for your business. OEE serves as a comprehensive performance metric that can be monitored to alter the way in which your shop floor performs.
- Identifying Downtime and Causes: OEE systematically categorises downtime into equipment failure, setup, or idling. By pinpointing the specific causes, manufacturers gain insights into which issues most frequently disrupt production. This detailed understanding allows for targeted improvements.
- Optimising Equipment Availability: One of the key components of OEE is availability, which measures the actual production time against the planned production time. Manufacturers can significantly increase the available production time by minimising downtime through preventive maintenance, efficient changeovers, and quick issue resolution, ensuring the equipment operates at maximum capacity.
- Enhancing Performance Efficiency: Performance OEE measures how close the equipment operates to its maximum speed. Manufacturers can identify and eliminate bottlenecks by analysing performance data, fine-tuning processes, and optimising machine settings. This leads to improved cycle times and higher output without compromising quality.
- Ensuring Quality Production: Quality is another vital component of OEE, measuring the ratio of good products to total products. OEE helps in identifying defects, errors, or rework. Manufacturers can implement corrective measures by understanding where and why defects occur, ensuring consistent, high-quality output. This reduction in defects minimises waste and improves overall product quality.
- Real-Time Monitoring and Decision-Making: Implementing OEE involves real time monitoring of equipment and processes. This live data allows for quick decision-making. Production managers can respond promptly to issues, adjust workflows, or allocate resources effectively. Real time insights enable proactive responses, preventing minor issues from escalating into major problems.
- Facilitating Predictive Maintenance: By analysing historical data, OEE can predict when equipment is likely to fail. This predictive maintenance approach allows for scheduled repairs and maintenance, preventing unexpected breakdowns. Predictive maintenance reduces downtime and prolongs equipment lifespan, optimising their efficiency in the long term.
- Improving Overall Business Efficiency: Optimising manufacturing efficiency through OEE directly impacts overall business efficiency by reducing waste, improving product quality, streamlining processes, and increasing customer satisfaction. Efficient operations translate into reduced costs, higher profitability, and a competitive edge in the market.
Why is it important to track Overall Equipment Effectiveness?
Tracking Overall Equipment Effectiveness (OEE) is essential for manufacturing operations as it provides a clear, data-driven understanding of equipment performance, availability, and quality. This insight allows businesses to identify bottlenecks, reduce downtime, enhance production speed, and improve product quality. By monitoring OEE metrics, companies can implement targeted strategies for continuous improvement, ensuring efficient resource utilisation, minimising operational costs, and maintaining a competitive edge. OEE tracking empowers manufacturers to make informed decisions, optimise processes, and maximise productivity, leading to increased profitability and operational excellence.
Steps for Incorporating OEE into Manufacturing Operations
Businesses can systematically integrate OEE into their manufacturing operations, enhancing efficiency, reducing downtime, improving product quality, and increasing profitability.
- Assessing your current Manufacturing processes: The initial step comprehensively evaluates your existing production processes. You need to understand how equipment operates, identify bottlenecks, and assess the overall efficiency of your manufacturing setup.
- Setting OEE Performance goals: Once you clearly understand your current processes, establish specific OEE performance goals that align with your business objectives. These goals should be realistic and measurable, serving as benchmarks for improvement.
- Collecting relevant data and measurements: To effectively track OEE, gather relevant data and measurements. This includes data on equipment uptime, performance metrics, and product quality. Implement data capture systems to collect the required information accurately.
- Analysing OEE data to identify improvement areas: Utilise the collected data to identify areas where performance falls short. Analysing OEE data lets you pinpoint issues like downtime causes, production bottlenecks, or quality problems.
- Implementing changes and continuous monitoring: Based on the insights gained from the analysis, implement targeted changes and improvements in your manufacturing processes. Whether it involves optimising equipment settings, implementing preventive maintenance, or streamlining workflows, make necessary adjustments. Importantly, establish a system for continuous monitoring OEE to ensure that improvements are sustained over time.
Data Collection Software for OEE tracking
Utilising data capture software to track Overall Equipment Effectiveness (OEE) is essential for precision and efficiency in manufacturing. A data collection software automates capturing and collecting relevant data, such as equipment uptime, production speeds, and quality metrics, ensuring accuracy and real time analysis. By efficiently capturing and processing this data, businesses can identify bottlenecks, minimise downtime, enhance performance, and improve overall operational efficiency.
How to Calculate OEE using Data Capture Software?
Calculating OEE metrics using data capture software involves systematically leveraging real-time data for accurate analysis. The data collection software automatically captures relevant data such as equipment downtime, production rates, and quality metrics. It calculates equipment uptime and production quality using machine data and performance metrics. The software consolidates this data and generates comprehensive reports, enabling manufacturers to identify inefficiencies, set performance benchmarks, and implement targeted improvements. Data capture software ensures precision and timeliness in OEE calculations, facilitating informed decision-making and driving continuous enhancements in manufacturing operations.
Tips for ensuring a smooth transition to OEE-driven efficiency
- Comprehensive Training: Invest in thorough training programs for your workforce to ensure everyone understands the principles of OEE and how to use the relevant tools and softwares effectively.
- Data Infrastructure: Establish a robust data capture and management infrastructure to ensure accurate and real-time data collection, storage, and analysis, facilitating informed decision-making.
- Clear Performance Goals: Set clear and achievable OEE performance goals that align with your business objectives, allowing you to measure progress and success accurately.
- Continuous Improvement Culture: Foster a culture of continuous improvement, encouraging employees to actively identify and implement efficiency enhancements.
- Regular Performance Reviews: Conduct regular reviews of OEE metrics, discussing findings and action plans with cross-functional teams to maintain a proactive approach to efficiency enhancement.
The impact of Overall Equipment Effectiveness (OEE) on manufacturing operations is immense. It has the power to transform the performance of your entire shop floor. By measuring and optimising availability, performance, and quality, OEE improves efficiency, reduces downtime, and enhances product quality.
As we move forward in the age of data-driven manufacturing, embracing OEE isn't just about improving processes; it's about ensuring sustained success. So, manufacturers, if you still need to incorporate OEE for your business, embrace it, integrate it into your operations and witness the incredible journey towards achieving operational excellence.