Capturing Real-time Manufacturing Data for Production Efficiency
August 23, 2023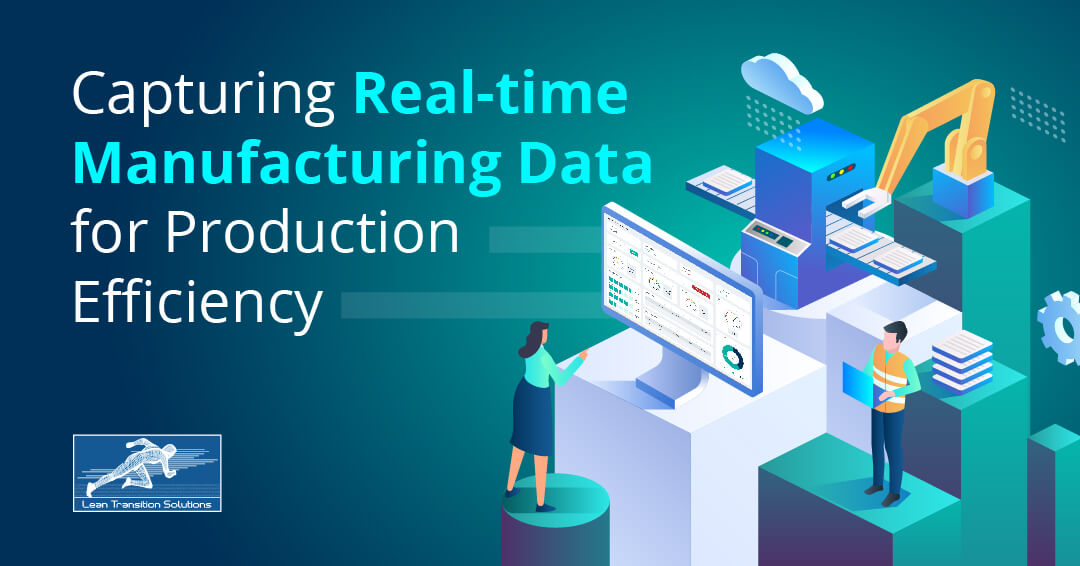
Modern manufacturing must emphasise the importance of production-line performance and growth. These twin pillars drive operational efficiency, competitive advantage, and sustainable success. A well-optimised production line ensures streamlined processes, minimised downtime, and maximum throughput. Fostering growth within the production line opens avenues for expanded capacities, improved product quality, and increased visibility in the global market.
Real-time manufacturing data collection significantly transforms production-line operations by facilitating real-time monitoring of machinery and processes, swiftly identifying bottlenecks, inefficiencies, and potential disruptions. With real-time data, decision-makers can easily adjust to optimise workflows, allocate resources efficiently, and prevent costly downtime.
Moreover, predictive analytics derived from real-time data aid in proactive maintenance, minimising disruptions and maximising overall production-line performance. Let's understand how real-time manufacturing data collection empowers agile decision-making and paves the way for operational excellence and enhanced productivity.
The Role of Real-Time Data Collection in Manufacturing
Real-time manufacturing data capturing refers to the continuous process of gathering and analysing data from various stages of the production process in manufacturing without any delay. It involves the integration of sensors, Internet of Things (IoT) devices, and monitoring systems that capture data directly from the production floor. These components form a network that feeds data to centralised systems for instant analysis.
Unlike periodic data collection, real-time data provides immediate insights, enabling swift responses to changing conditions. It allows for accurate monitoring of production-line activities, minimising the risk of defects and downtimes. Real-time data enhances transparency, giving stakeholders a real-time view of operations, which is crucial for decision-making.
Real-time data capture impacts manufacturing KPIs like OEE (Overall Equipment Efficiency), cycle times, production rates, and quality control indicators. Manufacturers can monitor and optimise these metrics in real time, identify underperforming areas, and make data-driven decisions to improve efficiency and performance.
Numerous industries can benefit from real-time data collection. Automotive tracks assembly line progress and manages inventory. In electronics, data identifies defects early. Food and beverage processing relies on data for quality control and regulatory compliance.
Implementation of Real-Time Manufacturing Data Collection Systems
- Hardware and Software Components: In the implementation of real-time manufacturing data collection systems, a robust combination of hardware and software components is crucial. Sensors and IoT devices act as the eyes and ears of the production line, capturing real-time data on machinery performance, process metrics, and environmental conditions. This data is then seamlessly channelled to data aggregation and storage solutions, where it is organised and made accessible for analysis. These solutions act as the system's backbone, ensuring that the continuous influx of data is structured, stored efficiently, and ready for further processing.
- Integration with Existing Manufacturing Systems: By seamlessly integrating with ERP systems, manufacturers gain a holistic view of their production environment, enabling real-time inventory management, demand forecasting, and resource allocation. Additionally, integrating MES platforms enhances production visibility, allowing for synchronised workflow management, timely order execution, and quality control. This interconnected ecosystem ensures real-time insights seamlessly influence decision-making at all levels, fostering streamlined operations and improved production-line performance.
- Data Security and Privacy Concerns: Protecting sensitive manufacturing data involves implementing encryption measures, access controls, and authentication protocols to prevent unauthorised access or data breaches. Furthermore, compliance with industry regulations ensures that data collection, storage, and sharing practices adhere to established standards, safeguarding both proprietary information and customer privacy. By prioritising data security and privacy, manufacturers can foster trust among stakeholders while leveraging the full potential of real-time manufacturing data to fuel growth and innovation.
Considerations while implementing a Manufacturing Data Collection system
- Data Overload: When implementing a manufacturing data collection system, it's crucial to guard against the potential pitfalls of data overload. While real-time data offers valuable insights, an excess of information can overwhelm decision-makers, hindering timely and effective responses. Implementing intelligent data filtering and visualisation tools helps streamline the flow of relevant information, enabling focused analysis and swift decision-making. By striking the right balance, manufacturers can harness the power of data without succumbing to information overload.
- Scalability and System Integration: The scalability of a data collection system is paramount to accommodate future growth and evolving demands. Compatibility with existing manufacturing processes and technologies is essential for seamless system integration. Implementing flexible architecture and modular components ensures the system can expand alongside production needs. This proactive approach avoids disruptions and optimises resource allocation as the manufacturing environment evolves, safeguarding sustained operational efficiency.
- Workforce Training and Adoption: Introducing a manufacturing data collection system necessitates proper workforce training and adoption strategies. Employees must be equipped with the skills to utilise the system effectively and interpret real-time insights. A comprehensive training program and clear communication about the system's benefits fosters a culture of data-driven decision-making. Manufacturers can ensure smooth adoption and maximise the system's potential by involving the workforce in the transition and addressing any concerns.
- Cost Implications and Return on Investment (ROI): Implementing a data collection system entails financial considerations that must align with expected returns. While upfront costs may include hardware, software, and implementation expenses, the potential for improved production-line performance, reduced downtime, and enhanced product quality can lead to a favourable return on investment. Manufacturers must conduct a comprehensive cost-benefit analysis to determine the system's feasibility and long-term growth potential, considering both tangible and intangible benefits.
Trends in Real-Time Manufacturing Data Collection
- Artificial Intelligence and Machine Learning Integration: The future of real-time manufacturing data collection lies in integrating Artificial Intelligence (AI) and Machine learning (ML). These technologies enable predictive maintenance by analysing historical and real-time data to anticipate equipment failures, reducing downtime. Additionally, AI-driven insights optimise production-line processes through adaptive algorithms, enhancing efficiency and resource utilisation. This synergy between real-time data and AI/ML drives smarter decision-making and propels manufacturing toward a more autonomous and data-driven future.
- Edge Computing and Fog Computing in Manufacturing: Edge computing and fog computing are emerging trends in real-time data collection for manufacturing. Manufacturers mitigate latency by processing data closer to the data source, ensuring real-time insights even in high-demand environments. This decentralised approach enhances data processing speed, minimises network congestion, and facilitates quick response times. As manufacturing becomes more complex and data-intensive, edge and fog computing enables efficient real-time data analysis at the point of action.
- Advancements in Predictive and Prescriptive Analytics: Real-time manufacturing data collection is evolving with increasingly sophisticated predictive and prescriptive analytics capabilities. Predictive analytics use past and present data to predict future trends and issues, enabling proactive decision-making. Prescriptive analytics, on the other hand, go beyond prediction by providing actionable recommendations to optimise production processes. By harnessing these advancements, manufacturers gain a competitive edge through precise resource allocation, minimised downtime, and maximised production-line performance.
Collecting manufacturing data in real-time is crucial for industrial success, combining operational flexibility with sustainable growth. Manufacturers can gain unprecedented insight into their operations by instantly capturing and analysing production data, machinery, and resources. This visibility in real-time allows for quick decision-making, enabling timely adjustments to optimise workflows, improve efficiency, and minimise disruptions.
Real-time manufacturing data collection streamlines production-line performance and elevates precision, productivity, and profitability. In this dynamic manufacturing era, utilising real-time data is crucial for operational excellence and building a strong foundation for the future.