How Manufacturers use Data to drive Value?
September 29, 2023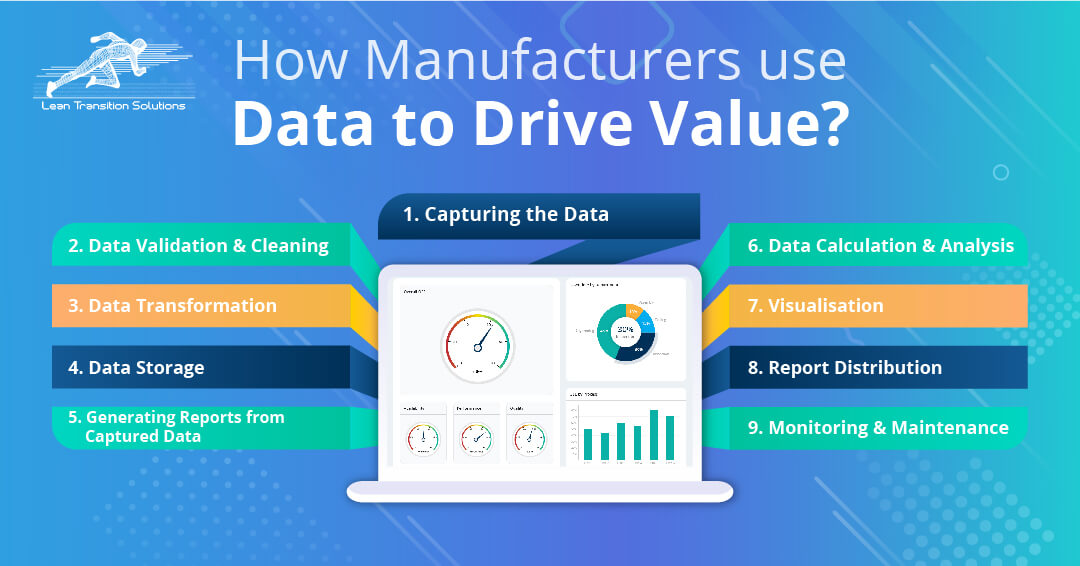
Data serves as the compass guiding decisions. It's more like a radar that spots opportunities or a key that unlocks innovation. Data collection can be a priceless asset in modern manufacturing that can transform business operations and drive value. Manufacturers must utilise data to identify and address inefficiencies, optimise overall processes, and make informed decisions.
In this digital age, where every move and every machine is a potential source of valuable insights, the significance of data collection software has significantly gained prominence. It stands at the forefront of a manufacturing revolution, bridging the gap between raw data and actionable intelligence. With the ability to seamlessly collect, process, and interpret vast volumes of data, data capture softwares has become a crucial component of modern manufacturing strategies, propelling organisations toward productivity, quality, and profitability.
Let's go ahead and take a closer look at the symbiotic relationship between data and manufacturing, delving into the vital role that data collection software plays in reshaping the industry. Data is not merely an asset but the catalyst propelling manufacturing into a future marked by precision, agility, and relentless innovation.
How Automated Data Collection Works?
Automated data collection refers to the process of gathering information without manual human intervention. It involves using technology, such as sensors, software, or devices, to automatically collect and record data from various sources, including machines, sensors, and digital systems.
This data can encompass a wide range of information, from production statistics in manufacturing plants to user interactions on websites. Automated data collection streamlines processes, reduces human error, and allows for real-time data analysis, making it a valuable tool in various industries, including manufacturing, healthcare, finance, and logistics.
Why is Data crucial for your Business?
When data is captured, it has a transformative power to drive efficiency, inform decision-making, and optimise processes across every facet of the manufacturing ecosystem. Manufacturers rely on data to gain real-time visibility into production processes, machine health and ensure product quality. It empowers predictive maintenance, allowing for timely interventions that prevent costly downtime.
Data is instrumental in meeting customer demands by fine-tuning production schedules and minimising lead times. Moreover, it fosters a culture of continuous improvement, enabling manufacturers to identify inefficiencies, reduce waste, and enhance overall operational performance. Data empowers manufacturers to remain agile, responsive, and competitive in a globalised and highly competitive market, paving the way for innovation and sustained growth in any organisation.
Data Collection Software and its relevance in Manufacturing Operations
Data capture software has emerged as a transformative force in modern manufacturing operations, revolutionising how businesses collect, manage, and leverage data to drive efficiency, quality, and competitiveness. In an era marked by digitalisation and Industry 4.0, the relevance of data collection software in manufacturing is more significant than ever. Manufacturing operations generate vast amounts of data that needs to be analysed to get shop floor insights.
The data contains vital information about machine performance, production rates, quality metrics, and inventory levels. Traditionally, capturing and analysing this data was tedious and cumbersome, relying on manual data entry or infrequent data sampling. However, data capture software has changed the game by automating and streamlining operational procedures and production schedules. Manufacturers can monitor operations in real time by integrating various sensors, machinery, and quality control checkpoints on the factory floor. This real-time visibility enables quick detection of anomalies, bottlenecks, or deviations from established quality standards.
Creating Value through Data Capture
Manufacturers can derive significant value from data by leveraging advanced analytics, IoT technologies, and machine learning to optimise production processes. This helps them reduce operational costs, improve product quality, and gain valuable insights into market trends. Manufacturers can enhance efficiency, stay competitive, and deliver higher-quality services by analysing collected data. Let's take a closer look at how organisations can employ data collection softwares to generate the value they seek:
- Production Process Optimisation: Manufacturers can collect data from sensors, machines, and production lines to monitor and optimise manufacturing processes. Capturing machine data can help identify bottlenecks, reduce downtime, improve resource utilisation, and enhance Overall Equipment Effectiveness (OEE).
- Quality Control: Data from quality control inspections and tests can be used to identify defects early in the production process, reducing waste and rework. Manufacturers can implement Statistical Process Control (SPC) techniques to maintain consistent product quality.
- Supply Chain Management: Capturing data from internal operations can improve supply chain visibility. Manufacturers can better manage inventory, reduce lead times, and make data-driven decisions to minimise supply chain disruptions.
- Predictive Maintenance (PdM): Manufacturers can implement Predictive Maintenance (PdM) strategies by utilising data from machine sensors and maintenance logs. This allows them to schedule maintenance activities proactively, reducing unplanned downtime and extending the lifespan of equipment.
- Energy Efficiency: Monitoring energy consumption data can lead to significant cost savings and reduced environmental impact. Manufacturers can identify energy-intensive processes and equipment and implement energy-efficient practices.
- Customer Feedback and Market Insights: Manufacturers can collect and analyse customer feedback and market data to better understand customer preferences, market trends, and emerging opportunities. This information can guide product development and marketing efforts.
- IoT and Smart Manufacturing: The Internet of Things (IoT) enables manufacturers to connect various devices and sensors to collect real-time data. This data can be used for process automation, remote monitoring, and improving overall production efficiency.
- Data Analytics and Machine Learning: Advanced data analytics and machine learning techniques can help uncover insights from large datasets. Manufacturers can use these insights for demand forecasting, quality prediction, and operations optimisation.
- Cost Analysis: Manufacturers can identify areas where cost reduction is possible by collecting and analysing cost-related data. This includes analysing labour costs, material costs, and overhead expenses.
- Regulatory Compliance: Manufacturing often involves strict regulatory requirements. Proper data collection and documentation can ensure compliance with industry regulations and standards.
- Product Lifecycle Management: Manufacturers can use data to manage the entire product lifecycle, from design and development to manufacturing and end-of-life. This helps make informed decisions about product updates, recalls, and discontinuations.
- Risk Management: Data can be used to assess and mitigate risks in manufacturing operations. This includes identifying potential safety hazards, supply chain disruptions, and financial risks.
Steps involved in Data driven Value with a Data Collection Software
Automated data collection software can calculate captured data to create reports that can be useful for businesses. Selecting software that aligns with your organisation's requirements and provides the necessary features for data capture, transformation, calculation, and reporting is important. Here's a general outline of the process:
- Capturing the Data: Automated data collection software collects data from various sources. The data can be in text, numbers, or in other formats. Standard methods of data capture include Optical Character Recognition (OCR), barcode scanning, data extraction from forms, web scraping, and integration with databases and APIs.
- Data Validation and Cleaning: The captured data may need to be validated and cleaned to ensure accuracy and consistency. The process involves checking for errors, removing duplicates, and standardising data formats.
- Data Transformation: The software may need to transform the captured data depending on the specific reporting requirements. The data collection software aggregates the collected data and performs calculations. Then, the output is converted into a suitable format for reporting.
- Data Storage: The captured and transformed data is typically stored in a structured database for easy access and retrieval.
- Generating Reports from Captured Data: Automated reporting tools generate reports from the captured and stored data. The software should allow users to define report templates, select data sources, and specify report parameters.
- Data Calculation and Analysis: To calculate data for reports, the software may use various mathematical and statistical techniques, such as:
- Summation and Aggregation: Adding up values, calculating averages, or performing other arithmetic operations on data.
- Data Modelling: Using statistical models to analyse and predict trends.
- Time-series Analysis: Analysing data over time to identify patterns and trends.
- Custom Calculations: Implementing specific calculations based on user-defined requirements.
- Visualisation: Data visualisation tools are used to create graphs to present the calculated data visually. Visualisation helps users better understand the data and its insight.
- Report Distribution: The reports can be easily shared through email, web portals, or print among all the stakeholders. Automated scheduling ensures that reports are generated and delivered regularly.
- Monitoring and Maintenance: Regularly monitoring the software and its data sources is essential to ensure accuracy and reliability. Maintenance includes updating data capture processes, handling changes in data sources, and addressing any issues.
Manufacturers today are producing goods and crafting insights from data streams that optimise processes, enhance product quality, and drive innovation. They create value far beyond the factory floor by harnessing advanced analytics, IoT technologies, and machine learning.
In short, data isn't just a resource for manufacturers; it's the engine that powers their journey toward a brighter and more prosperous future. Data-driven decision-making has become the cornerstone of success, allowing manufacturers to stay competitive, reduce costs, and, most importantly, better serve their customers. As we move forward in this modern manufacturing era, the possibilities for manufacturers are limitless, promising continued efficiency, sustainability, and product excellence advancements.