Role of Machine Monitoring in Enhancing Productivity
April 24, 2023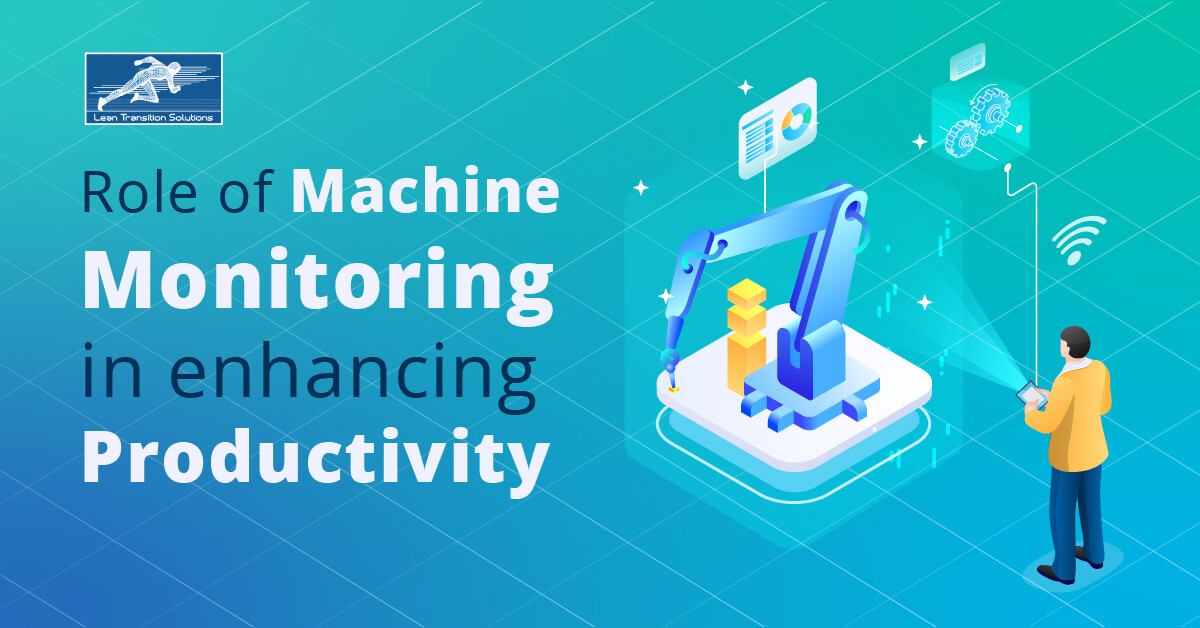
Every manufacturer is looking for ways to improve productivity. Machine monitoring is one of the most effective ways to achieve this goal. Let's explore how machine monitoring can improve productivity in your business.
Why Machine Monitoring is important for Productivity?
Machine monitoring tracks machine performance in real time. It can include tracking factors such as machine uptime, downtime, cycle time, and more. Machine monitoring provides manufacturers real-time data to make informed decisions about machine performance and productivity. Machine monitoring can also detect anomalies and alert operators when an issue arises. Research shows an average manufacturer experiences around 800 hours of equipment downtime annually. To reduce equipment downtime, manufacturers should invest in machine monitoring technology. Additionally, machine monitoring can help manufacturers improve Overall Efficiency.
Benefits of Machine Monitoring within a Production environment
Machine monitoring can provide manufacturers with real-time visibility into their machines' performance. Monitoring the performance of machines offers a wide range of benefits, including:
Identifying Issues: Manufacturers can monitor their machines in real-time and identify issues as they happen. Hence they can take action immediately to prevent downtime. For example, by analysing data from sensors on a machine, the manufacturer can detect that the machine is running hotter than its optimal temperature. It enables them to prevent a breakdown.
Increased Efficiency: The efficiency of your productivity is directly dependent upon your ability to monitor its normal operations. Machine monitoring helps to detect anomalies in machine functioning. When such issues are detected accurately and quickly, they can be fixed promptly, leading to a considerable improvement in the production process.
Centralised Data: Machines can be monitored and the data obtained can be centralised into a single platform. It permits access to data from multiple machines and identifies patterns and trends. By doing so, they can look for correlations between machines and processes, or even compare performance between different production lines or sites.
Historical Data Analysis: Manufacturers can access historical data analysis through machine monitoring. So, it is possible to identify patterns in machine performance and make informed decisions for future improvements. For instance, in the automotive industry, data analysis of past machine performance can be used to identify recurring issues, leading to more reliable products in the future.
How can Machine Monitoring aid in improving Productivity?
Machine monitoring can boost productivity in numerous ways. Now let's see various ways to make machine monitoring work for your business.
Real-Time Monitoring: Through monitoring machines in real-time, manufacturers can quickly identify issues that can be impacting productivity. For example, if a machine is experiencing frequent downtime, it is possible to send alerts to the manufacturer so they can take action to resolve the issue.
Preventing Downtime: Machine monitoring has predictive maintenance capabilities allowing manufacturers to identify and address issues before they become significant problems. It reduces downtime and increases machine uptime, leading to improved productivity.
Optimising Production: Monitoring machine performance can help manufacturers optimise their production processes by analysing historical data. For example, if a machine is consistently underperforming the Root Cause Analysis (RCA) can suggest improvements to optimise production.
OEE tracking: Overall Equipment Effectiveness (OEE), a metric used to track machine uptime, performance, and quality, can be tracked through monitoring machines. Organisations can identify areas for improvement and optimise their production processes by monitoring OEE, which boosts productivity.
Cycle time analysis: Machine monitoring allows manufacturers to track and analyse cycle times, which is the time it takes for a machine to complete a production cycle. Manufacturers can identify bottlenecks and optimise their production processes, improving productivity through analysing cycle times.
Enhancing Communication: Through centralising information obtained from machine monitoring, communication can be improved between different departments. For example, if a machine is experiencing issues, the maintenance department can be alerted so they can take action to resolve the issue.
Machine monitoring is essential to improving productivity in today's manufacturing environment. Shop floor data capture softwares offer manufacturers various benefits, including real-time tracking, customisable dashboards, automated alerts, and historical data analysis. Through monitoring machine performance, manufacturers can identify issues, prevent downtime, optimise production, improve maintenance, and enhance communication. Ultimately, this can improve productivity and profitability for the manufacturing organisation. Manufacturers can use real-time data and insights to make informed decisions and take proactive measures to improve their operations. Proper performance monitoring can help them stay competitive, meet customer demands, and achieve long-term success in the highly competitive manufacturing industry.