Manufacturing Shop floor Data Collection Software: Data-driven journey towards seamless production
November 14, 2024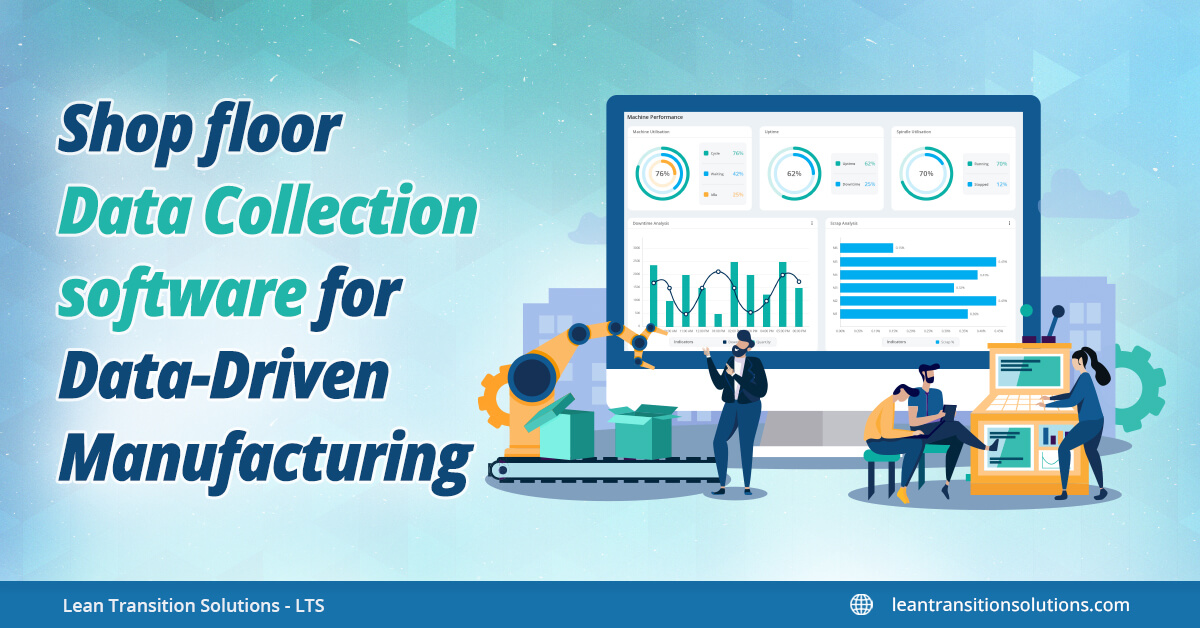
The pursuit of incompetence is a never-ending process in manufacturing; without it, companies lose track of their production. Data gathering and analysis are fundamental to driving towards efficiency, which has the immense ability to make informed decisions and streamline operations. However, the manual data collection process, which takes a tremendous amount of time, labour and resources, is not a good fit for an organisation that needs a well-audited data collection strategy.
Automated shop floor data collection software, the potential substitute for the complex manual process, helps companies get enhanced visibility into their entire production process. By automatically gathering data, the software delivers information about every key production metric, machine status, parts count and operational history. The manufacturers can see improved productivity and experience rapid value creation by implementing effective Shop Floor Data Collection Software.
Data-Driven Manufacturing: The Road to Success
Data is one of the crucial resources for every business. Rather than depending on unreliable data from the manual declaration, adopting an automated data-driven manufacturing strategy boosts throughput and profitability instead of merely yielding vague outcomes.
The manufacturing landscape is reshaped by data-driven approaches that provide valuable insights into the production process using real-time and historical data. Traditional production monitoring methods are falling short in encountering the complex and dynamic nature of modern manufacturing operations.
The significant decisions that drive the manufacturing process should always be generated from real data, not guesses or theories. Automated real-time data collection software, one of the vital elements of the next wave of manufacturing, is in tremendous demand due to its potential ability to drive and enhance the productivity of an organisation.
Why is Automation Critical in Manufacturing Data Collection?
Automated data collection refers to the utilisation of digital technologies to gather data from various systems such as manufacturing execution systems (MES), GPS systems, connected sensors and execution systems.
Shopfloor Data Collection Software is a computerised system for the collection and storage of quantitative and qualitative data from the production process. As practitioners of Lean Manufacturing know, finding and driving out waste is the base of successful manufacturing. Automation accelerates the identification of things that are happening on the shop floor, which opens more ways to enhance overall productivity by eliminating waste.
The Shopfloor data collection software collects two types of data: machine data and production data. Generating insights about these Key Performance Indicators (KPIs) contributes more to the existing body of knowledge through practical measurements.
Some of the examples of data that can be collected by the software are given below.
Machine data:
Maintenance records
System log data
Equipment diagnostics logs
Energy consumption
Temperature data
Geotag data
Production data:
Production rate
Output volumes
Yield rate
Average cycle time
Defect rates
Order fulfilment rates
Raw resource consumption
Utility consumption
Top Features of Shop Floor Data Collection Software
Detailed reports
Quality assurance
Root cause analysis
KPI analysis
Visual boards
Predictive maintenance
Touch screens and barcode scanning
Full audit traceability
Why is Shop floor data collection essential for production tracking?
Let's understand the value of Shop Floor Data Collection Software by analysing the types of data it gathers from the production place. The software collects the data, which has incredible value on the shop floor, and transfers it to meet your output goals.
Downtime
Help the managers to analyse Key performance indicators like Mean Time to Repair (MTTR) and Mean Time Between Failures (MTBF)
Aids to optimise maintenance schedules by understanding machine performance
Historical downtime data provides insights for reducing downtime
Get a clear picture of what machine needs upgrades and where to allocate resources
Reduced downtime leads to minimising operational and maintenance costs
Performance to schedule
Tracking performance to schedule ensures that production stays on target
Reduce late deliveries
Helps managers to address delays and makeshift priorities
Better resource allocation and minimise late deliveries
Changeovers
Accurate and real-time data helps to identify the inefficiencies in the setup process
Helps to implement fast Changeover techniques
Reduce idle time and increase throughput
First Quality Pieces
Aids in understanding the efficiency of the process
Lower first-pass yields indicate issues with operator performance, machine setup and material consistency
Helps to increase initial quality
Helps to reduce scarp rates
Maintenance breakdowns
Allow the organisation to establish prescriptive or predictive maintenance
Helps to track machine reliability
Reduce maintenance costs
Prioritise critical machinery
Improve maintenance schedule
Scrap
Helps to identify the patterns in production issues
Categories the defect causes into operational errors, machinery faults or material defects
Reducing scrap lowers operational costs
Enhances material usage
Reducing waste increases the overall efficiency
Work in Progress (WIP) Inventory
Helps manufacturers to optimise production flow
Aids identification of bottlenecks
Balance workloads across the production line
Ensure smooth operations by reducing lead times
Downtime is the failure of a machine to work, which halts production. The data collection software records and categorises the downtime for stoppage, jams, slowdowns, cleaning and other reasons. Any deviation from the normal operational parameters can be detected by the data collection software, which can record the cause, duration, and frequency of downtime.
Shop floor data collection software provides details about production orders within the established delivery times. This tracking picturises the production in relation to its scheduled runtimes and helps to meet the times. If there is any deviation from the plan, the software alerts the team and leaders to follow the predefined schedule.
Changeover time is the duration of the process of changing a production line from one product to another. Data collection software tracks equipment setup and adjustments. By automatically recording the total time spent on each changeover, it can analyse the machine stops and restarts.
First Quality Pieces is the production of a defect-free product on the first attempt. As a metric for assessing manufacturing efficiency, the percentage of usable products at the start is evaluated using the data collection software. The software counts the first batch of defect-free products that pass quality checks. The integration with the quality control equipment enhances the applicability of this process.
Data collection software monitors the types of maintenance breakdowns and their causes as per the maintenance teams and service orders. The sensors integrated into the machines detect the malfunctions instantly and automatically log the event when a breakdown occurs.
Scraps are waste or faulty products due to issues in the production process. Data collection software can track the number of defects and their types. Reducing the scrap rate is an important aspect of manufacturing, and the software provides better visibility by focusing on the production line.
Work in Process (WIP) describes partially finished goods awaiting completion. Too much WIP creates bottlenecks in production, and too little signals insufficient production capacity. Data collection software shows the efficiency of the production process by tracking the status and movement of WIP. It records the amount of WIP inventory at different stages by monitoring each workstation.
Embrace Shopfloor Data Collection Software for Competitive Advantage in Manufacturing Facility
Connecting your machines with the data collection software will provide you with a niche of invaluable information in order to enhance your production process. With an omniscient view of your shop floor, manufacturers can quickly deal with an organisation's working environment, maintenance and human capital. Factories that rely on outdated techniques and automation systems will not be able to function as efficiently as they could. Make an appropriate investment in the best shop floor data collection software that assists you in cutting down on laborious manual choices.
Having a shop floor data collection software that understands your functionalities and requirements will help you recognise and drive out waste. Janus Data Capture, the shopfloor data collection software by LTS, is a flexible system that can grow with your business needs and has immense capabilities to work with your operations. With Janus, manufacturers can drive a data-driven production planning approach, which contributes to achieving cost efficiency, productivity, quality and a successful position in the highly competitive manufacturing industry.
FAQs
1. What is the purpose of data collection software?
Automated shop floor data collection software is a potential substitute for the complex manual process and helps companies get enhanced visibility into their entire production process. It automatically provides information about every key production metric, machine status, parts count, and history.
2. What are the benefits of using shop floor data collection software?
Aids to understand the process
Greater KPI analysis
Visualise patterns in production issues
Helps to track machine reliability
Helps managers to address delays and makes solutions
Reduce maintenance costs
Reduced downtime and scrap rate
Optimise maintenance schedules
Better resource allocation
Increase overall efficiency
3. What is the data-driven manufacturing process?
Data-driven manufacturing is the process of making decisions based on the collected data. The data can be collected directly from the shopfloor manually or automatically using digital tools. The manufacturers use the collected data to make strategic moves to achieve their organisational objectives.
4. Why do manufacturers depend on automated data collection software?
Automated data collection refers to the utilisation of digital technologies to gather data from various systems such as manufacturing execution systems (MES), GPS systems, connected sensors and execution systems. It provides accurate, real-time data to drive towards efficiency.
5. What is an example of automated data in manufacturing?
In manufacturing, Machine Monitoring Systems can be considered an example of automatic data collection. These systems data, such as downtimes, runtimes, and cycle counts, are from production equipment. All this data will be loaded into centralised systems for performance tracking.