Improving Shop Floor Efficiency with Real-time OEE Monitoring
April 12, 2024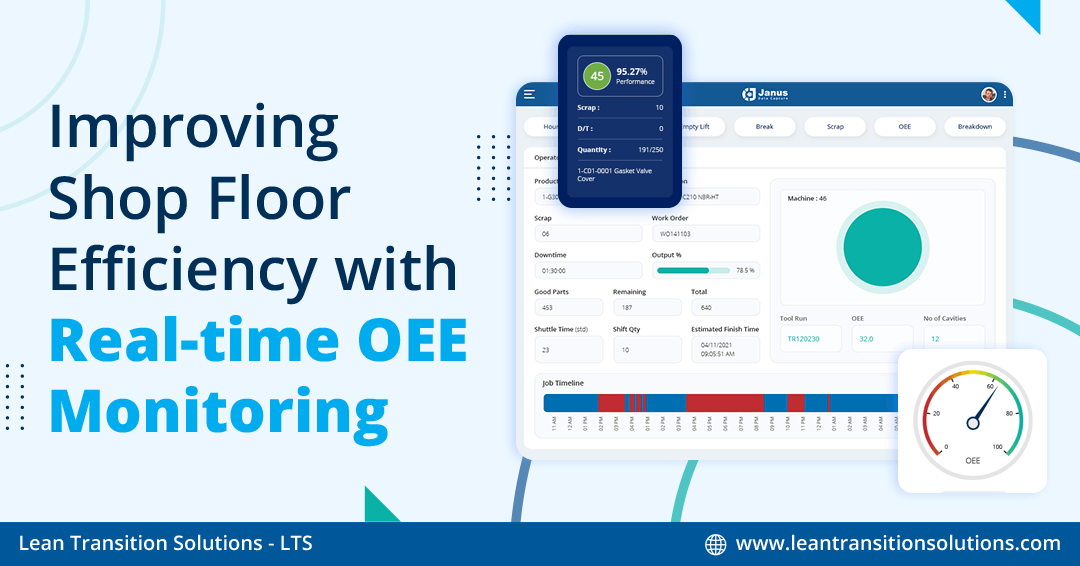
When your deliveries aren't meeting deadlines, it's easy to feel the pressure mounting. Unplanned downtime when a machine fails unexpectedly, production rejects resulting from quality issues, or any other disruptions in your operational performance might have put you amidst these missed deadlines with severe consequences.
In such critical moments, the importance of real time monitoring of the overall shop floor efficiency becomes evident. That's where real-time Overall Equipment Effectiveness (OEE) tracking steps in as your ultimate solution.
Real-time OEE tracking and monitoring using automated data collection software helps you make data-driven decisions and set the best performance benchmarks for your shop floor. Let's understand more about why manufacturers prioritise and track real-time OEE (Overall Equipment Effectiveness) to improve shop floor efficiency and avoid scenarios where they miss a deadline.
What is OEE?
Before moving on to the OEE improvement strategies, it is essential to know what OEE is. Overall Equipment Effectiveness (OEE) is a crucial performance metric that is used to evaluate the efficiency of manufacturing processes within the shop floor. In other words, OEE is a performance benchmark or indicator that can track the efficiency of your shop floor processes.
OEE data collection helps provide insights into equipment health and its real-time conditions by measuring equipment availability, performance, and product quality. Real-time OEE considers downtime, speed losses, and defects to determine the overall productivity of machinery for optimising production processes and maximising output.
By improving OEE in real-time, businesses can identify improvement areas, reduce waste, and enhance operational performance to achieve higher levels of shop floor efficiency and profitability.
Improving OEE Factors for Shop floor Efficiency
Availability: Availability in OEE is a factor that refers to the percentage of time that equipment is available for production or manufacturing processes. It is a critical factor as it directly impacts overall productivity and, hence, the efficiency of your shop floor. By minimising downtime and ensuring machines are operational when needed, businesses can maximise output and meet production targets effectively. How is that possible? Tracking real-time OEE using an OEE monitoring system enables proactive identification and resolution of machine or equipment issues, reducing downtime and improving overall equipment availability.
Performance: As an OEE factor, performance measures how efficiently equipment is operating in terms of speed and productivity. Understanding these metrics is essential for optimising production processes with the shop floor and maximising throughput. Real-time OEE data monitoring plays a key role in this aspect, allowing businesses to identify opportunities for enhancing machine speed and overall equipment performance. By monitoring OEE performance in real-time, companies can make necessary adjustments or replace equipment or spare parts to improve efficiency and achieve higher production rates.
Quality: Quality is a factor of OEE, ensuring that products meet specified standards and customer expectations. Maintaining product quality on the shop floor is important for reputation and customer satisfaction. Monitoring OEE in real time to analyse quality enables businesses to detect defects early in the production process, minimising waste and rework. By continuously monitoring production from real-time OEE insights, companies can promptly identify deviations from standards and take corrective actions after analysing their root causes to uphold product quality and consistency.
Calculating OEE score - Is it necessary for your Shop floor?
In his seminal work, 'Introduction to TPM' (1984), Seiichi Nakajima introduced the concept of a world-class OEE score, setting a benchmark for manufacturing excellence. Nakajima's definition of world-class OEE specifies a score exceeding 85%.
This benchmark represents the pinnacle of operational efficiency and performance within the Total Productive Maintenance (TPM) framework. Attaining such an OEE score signifies optimal utilisation of resources or machines with minimal downtime and maximum productivity. Manufacturers aspire to achieve this standard, reflecting their commitment to continuous improvement and excellence in production processes.
You can calculate your OEE score using the following formulas. After calculating your availability score, performance score and quality score separately; you are ready to calculate your overall OEE score.
Availability = Runtime / Planned Production Time.
Performance = (Ideal Cycle Time × Total Count) / Run Time.
Quality = Good Count / Total Count.
OEE Score = Availability X Performance X QualityFor Example, if a shop floor achieved an availability score of 95%, performance score of 95% and Quality score of 95% then their OEE score will be 85.7%.
OEE = 95% x 95% x 95% = 85.7%
What does your OEE score mean?
The OEE scores typically observed in manufacturing operations usually fall within the range of 65% to 85%. This range serves as a practical benchmark for evaluating operational efficiency and performance across various industries.
Manufacturing plants with an OEE score below 65% often indicate significant blockages in their manufacturing productivity. Such OEE scores may signal inefficiencies stemming from factors like downtime, unoptimised equipment utilisation, or quality issues.
Tips for improving your OEE score!
Monitor and Address Inconsistent Part Quality: Implement a system to continuously monitor part quality and promptly address any inconsistencies to improve the OEE value.
Ensure Adequate Labour Resources: Prevent labour shortages by optimising staffing levels to maintain smooth operations and enhance lean OEE.
Eliminate the Six Big Losses: To boost OEE, identify and eliminate the six major sources of productivity loss—Unplanned Stops, Planned Stops, Small Stops, Slow Cycles, Production Rejects, and Start-up Rejects.
Prioritise Predictive Maintenance: Incorporate predictive maintenance practices to anticipate equipment failures and minimise unplanned downtime, thus maximising OEE value.
Automating OEE tracking for improved shop floor efficiency
Manual OEE calculations are prone to errors and often fail to provide accurate insights, limiting their impact on shop floor efficiency. Relying on manual methods for OEE measurement can result in discrepancies and inconsistencies, hindering the ability to make informed decisions and, hence, drive meaningful improvements. However, by automating real-time OEE tracking, businesses can overcome these challenges and unlock substantial benefits.
With automated data collection software, organisations can seamlessly monitor and track OEE metrics across equipment availability, performance, and production quality. These automated data capture systems offer interactive OEE dashboards, visualising detailed OEE data on machine utilisation, speed losses, and product defects based on real-time shop floor processes.
By using automated real-time OEE tracking and monitoring softwares, companies can identify inefficiencies, minimise downtime, and optimise production processes precisely. Detailed OEE reports generated based on shop floor performance help in proactive decision-making, empowering organisations to foster continuous improvement and achieve peak operational performance.
If you are still wondering how to set up an automated data collection solution on your shop floor for real-time OEE tracking, it is simpler than you might think! The following steps simplify the implementation of automated data collection software on your shop floor.
1. Research and Select Software: Choose automated data collection software with real-time OEE monitoring capabilities that match your organisational needs. The Automated OEE tracking system must also generate customisable OEE reports and should be compatible with existing systems.
2. Ensure System Integration: Integrate the automated data capture software seamlessly with existing manufacturing systems and equipment for accurate real-time OEE tracking.
3. Provide Staff Training: Train your employees comprehensively on software functionalities, data interpretation, and troubleshooting.
4. Implement Real-time OEE Monitoring: Use the real-time OEE monitoring and tracking feature of automated data collection software to continuously track OEE across availability, performance, and quality metrics and promptly identify deviations.
5. Establish Feedback Channels: Enable staff to provide insights and feedback based on real-time OEE data to foster collaboration and improvement.
6. Review and Analyse OEE Data: Regularly evaluate captured OEE data to identify trends, patterns, and areas for improvement.
7. Foster Continuous Improvement: Utilise OEE tracking data to drive ongoing improvement initiatives, optimise processes, and enhance equipment effectiveness.
Benefits of Real-time OEE tracking
Reducing Downtime: Real-time OEE monitoring helps identify and address issues promptly, minimising unplanned downtime.
Identifying Equipment Inefficiencies: By tracking OEE in real-time, businesses can pinpoint inefficiencies in equipment performance and take corrective actions.
Optimising Production Processes: Real-time OEE tracking enables continuous optimisation of production processes to maximise output and efficiency.
Improving Asset Utilisation: Monitoring OEE in real-time allows for better asset and resource utilisation, improving overall efficiency.
Boosting Overall Equipment Reliability: By monitoring OEE in real-time, organisations can improve equipment reliability and reduce the likelihood of breakdowns.
Setting Performance Benchmarks: Real-time OEE analysis facilitates the establishment of performance benchmarks for continuous improvement initiatives.
Data-Driven Decision Making: Real-time OEE data provides valuable insights for making informed decisions and driving operational improvements.
Minimising Waste and Rework: By monitoring OEE in real-time, businesses can identify and address issues related to product quality, minimising waste and rework.
Enhancing Labor Productivity: Real-time OEE monitoring helps optimise workforce productivity by identifying and addressing bottlenecks in production processes.
Increased Profitability: Monitoring and tracking real-time OEE contribute to increased profitability through improved efficiency, reduced downtime, and optimising resource utilisation.
Wrapping up this session, we know that real-time OEE tracking offers a transformative solution for increasing shop floor efficiency. By leveraging automated data collection and monitoring systems, businesses can identify and eliminate issues as they arise, proactively improving operational performance.
The shift from manual data entry to real-time OEE monitoring provides instantaneous insights into machine performance, availability, and quality metrics, enabling organisations to stay ahead of potential problems, minimise downtime, and maximise productivity.
Embracing streamlined real-time OEE monitoring eliminates data redundancy, inconsistencies and errors associated with manual data entry, ensuring accuracy and optimisation of shop floor operations. With an automated data capture system, businesses can confidently navigate towards greater efficiency, competitiveness, and success in the dynamics of their manufacturing landscape.