Empowering Equipment Health with Shop Floor Data Collection Software
January 29, 2025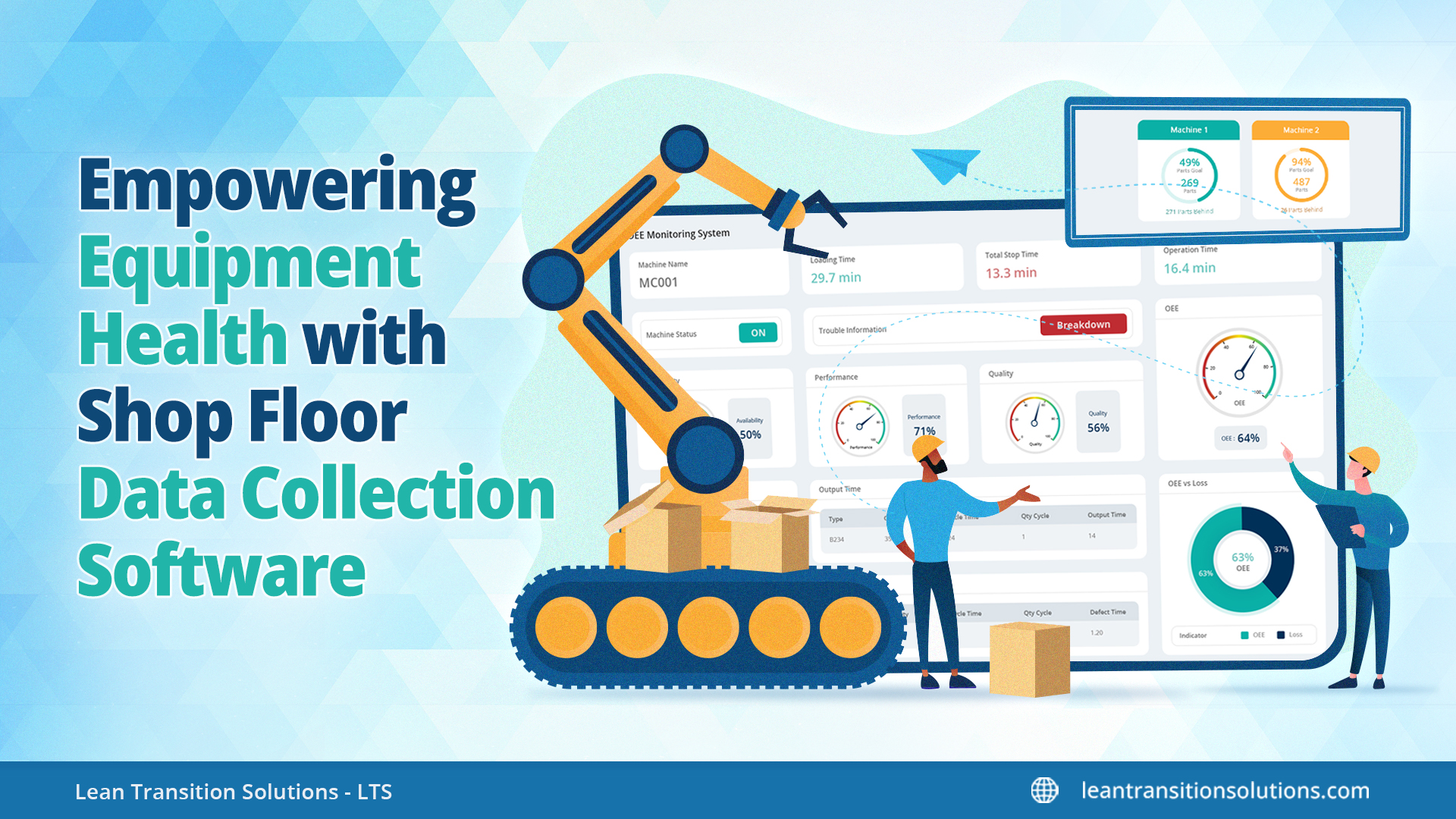
The shop floor is a crucial aspect of manufacturing that has always been associated with a high degree of efficiency and precision as the key factors of success. However, can you imagine the shop floor giving you detailed information on what it requires for its efficient operation? Well, using modern shop floor data collection software, that’s no longer a distant dream, but a reality.
By adopting data capture and analysis directly from the machines, these systems enable manufacturers to make informed decisions about the health of their assets in real time. The result? Better equipment health monitoring, more intelligent choices, less failure, and unmatched efficiency. Now let us delve into how this disruptive technology is revolutionising manufacturing.
By adopting data capture and analysis directly from the machines, these systems enable manufacturers to make informed decisions about the health of their assets in real time. The result? Better equipment health monitoring, more intelligent choices, less failure, and unmatched efficiency. Now let us delve into how this disruptive technology is revolutionising manufacturing.
Why is machine health monitoring important?
Equipment is the heart and core of manufacturing businesses. Like an investment, it stimulates production, guarantees operations and is accorded a direct measure of profitability. Being a critical part of successful production, machine health monitoring takes corrective and preventive action by diagnosing equipment performance. It aims for the effective working of the machine to meet the industry demands.
The benefits of machine health monitoring include
Classic and condition-based machine monitoring gives useful information concerning the health of the machines but is best enhanced by the implementation of automated data collection systems on the shop floor. This software is a real-time information aggregator and processor, meaning that it identifies and gathers data on machines. It operates at a basic level of logs of traditional machines and also collects more advanced information such as vibration and temperature data from condition-based monitors.
The benefits of machine health monitoring include
- Offer data-driven insights
- Prioritise maintenance operations
- Aids forecasting
- Helps to schedule
Classic and condition-based machine monitoring gives useful information concerning the health of the machines but is best enhanced by the implementation of automated data collection systems on the shop floor. This software is a real-time information aggregator and processor, meaning that it identifies and gathers data on machines. It operates at a basic level of logs of traditional machines and also collects more advanced information such as vibration and temperature data from condition-based monitors.
Transforming Equipment Monitoring in Manufacturing with Shop floor data collection software
Traditionally, equipment health monitoring was done through manual, on-demand observations, which caused downtime and lower effectiveness. Fast forward to Industry 4.0 where manufacturers use automated systems for data collection of their assets. Automatic shopfloor data collection software uses real-time data analytics, IoT and machine learning to continuously monitor performance. By leveraging this data, businesses can transition from reactive to proactive management. Let's explore.
Role of IoT, Sensors, and Machine Controls in Data Integration
Indeed, the essence of this system is IoT devices and sensors that collect information from modern and conventional tools.
Role of IoT, Sensors, and Machine Controls in Data Integration
Indeed, the essence of this system is IoT devices and sensors that collect information from modern and conventional tools.
- As a result of IoT technology, it is possible to let all the devices, software platforms, and operators exchange data with each other, and with the cloud.
- Legacy equipment is the older machines or devices that were not originally designed with modern connectivity or digital integration. But using the sensors attached to the legacy metrics, any physical parameter such as temperature or vibration can be read and acted upon. Each of these signals is relayed to the data collection system which processes it and presents it in real-time.
- Machine controls, on the other hand, are part of the most contemporary machines. These systems gather crucial operational data from the components of the machine in real-time hence no need for data entry or regular monitoring. It constantly measures machine health indicators including energy consumption, water level, and speed and transfers this data in real-time. This machine control data is vital for improving overall equipment effectiveness (OEE), identifying bottlenecks and predictive maintenance.
Key Tactics used by Shop floor data collection software for effective Equipment Monitoring
- Predictive Maintenance: Optimise the advanced analysis to anticipate the equipment failures and fix the probabilities before they turn into reality. This saves on costly repair bills and also reduces cases of production downtime.
- OEE (Overall Equipment Effectiveness) Optimisation: Use the data to determine operational effectiveness and inefficiencies with OEE indicators. This aids in identifying areas of inefficiency and in enhancing the productivity of used equipment and human resources.
- Real-Time Monitoring: Track Key Performance Indicators (KPIs) like speed, temperature, pressure and vision continuously to detect irregularities quickly. This lowers the major failure risks.
- Root Cause Analysis: Get to the root cause by further analysing the data, allowing manufacturers to address the root of concern, not just its visible signs.
- Automated Notifications and Alerts: Establish several limits for the key metrics, if a machine crosses these limits, the system issues alarms at once. This makes it easier to avoid risks and issues which might grow to be expensive.
- Energy Consumption Monitoring: Shop floor data collection software also assists the organisation in tracking the energy consumption of the manufacturing process to ensure that there is efficient use of energy and cut down on any wastage.
- Improved Reporting and Documentation: An automated system creates accurate maintenance and production reports by eliminating human errors. It also offers proof that may be useful in the process of compliance and auditing.
- Cross-Platform Integration: For a seamless flow of information across departments, data collection software integrates with ERP, MES and SCADA which help the decision makers to create accurate data-driven decisions.
Impact of Shop Floor data collection software on Manufacturing efficiency
- Enhancing Quality Control Through Data-Driven Insights
With real-time data, the manufacturer can be able to monitor other factors such as the spindle speed or the tool wear to produce quality products.
For example, an automobile manufacturing plant might use real-time data collection software installed on the shop floor to track the accuracy of welding machines thereby minimising flawed production and resultant rework costs. - Minimising Downtime and Maximising Productivity
Automated system detects anomalies like excessive vibrations or temperature spikes.
For example, a manufacturing plant that has IoT sensors on CNC machines can organise regular maintenance to prevent the failure of critical parts, hence pulling an unplanned break. - Improved Workforce Efficiency
Instead of tracking machine performance manually, supervisors and operators can concentrate on high-value tasks by automating the data collection process.
For example, automated reporting tools give a dashboard summary of machine health that cuts down on paperwork. It reduces administrative workload and increases decision-making speed. - Cost-Saving Benefits of Proactive Maintenance
Using the historical and live data the predictive maintenance system anticipates the attention needed for the equipment.
For example, replacing the machine parts by analysing the data collected from software avoids costly downtime and emergency repairs. - Streamlined Inventory Management
Automated systems can help link production information with inventory, to make certain that raw materials are restocked when needed.
For example, the system triggers automated reorders when inventory levels drop below a pre-defined limit. - Improved Energy efficiency
Energy consumption data enables manufacturers to find out the areas which consume more energy.
For example, supervising a production line may point out that some machines are on while they are not in use.
Embrace the Future of Equipment Health Management with Janus Data Capture
Automated data collection software has revolutionised how manufacturing companies track and manage their assets. These systems combine IoT, sensors, and industrial machine controls by providing real-time monitoring and driving real-time and predictive maintenance solutions.
Modern manufacturing demands advanced tools that deliver precision, efficiency and cost-effectiveness. To fully leverage these advancements, Janus Data Capture emerges as the ultimate solution. Janus acts as an effective tool for collecting shop floor data so that inefficiencies, resource management, and quality improvements can be identified and endorsed. Whether you operate legacy machines or cutting-edge systems, Janus provides optimal visibility and control. So that you can make possible decisions for future improvements. Make the leap to smarter manufacturing with Janus.
Modern manufacturing demands advanced tools that deliver precision, efficiency and cost-effectiveness. To fully leverage these advancements, Janus Data Capture emerges as the ultimate solution. Janus acts as an effective tool for collecting shop floor data so that inefficiencies, resource management, and quality improvements can be identified and endorsed. Whether you operate legacy machines or cutting-edge systems, Janus provides optimal visibility and control. So that you can make possible decisions for future improvements. Make the leap to smarter manufacturing with Janus.
FAQ’s
1. What is the purpose of equipment monitoring?
The purpose of equipment monitoring is to avoid emergency breakdown that causes a stoppage of production. It also aims to enhance the life of equipment and take corrective actions before the escalation of issues. It also helps the companies to optimise their performance.
2. How to automate shop floor data collection?
By implementing an effective shop floor data collection software, the data can be collected, stored and analysed with real-time insights.
3. What is shop floor software?
Shop floor software is a tool that handles production orders through automation and real-time data monitoring. It also monitors progress, handles production orders, reduces hazards and boosts productivity.
The purpose of equipment monitoring is to avoid emergency breakdown that causes a stoppage of production. It also aims to enhance the life of equipment and take corrective actions before the escalation of issues. It also helps the companies to optimise their performance.
2. How to automate shop floor data collection?
By implementing an effective shop floor data collection software, the data can be collected, stored and analysed with real-time insights.
3. What is shop floor software?
Shop floor software is a tool that handles production orders through automation and real-time data monitoring. It also monitors progress, handles production orders, reduces hazards and boosts productivity.