Developing a Data Strategy to improve Manufacturing Processes
February 13, 2024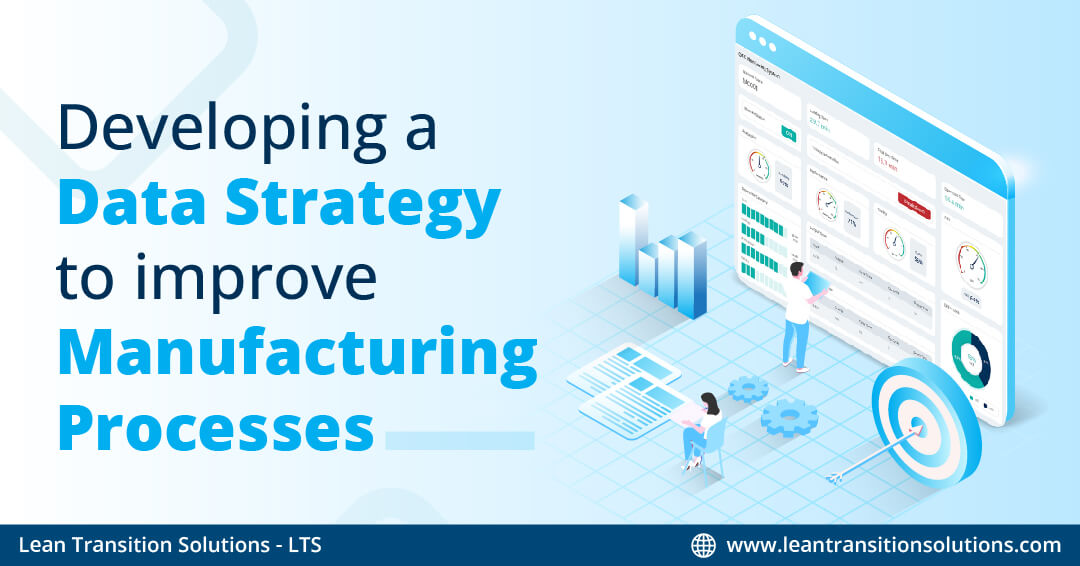
Over many years, manufacturers have relied on papers or spreadsheets for collecting machine data across diverse operational processes. However, as we progress into an era driven by technological advancements, the dynamics of data strategy in manufacturing are undergoing a deep shift.
The advent of AI (Artificial Intelligence) and Data Collection software solutions has ushered in a new dimension in data collection processes, challenging traditional methods and offering transformative opportunities. This blog explains how manufacturers use advanced data collection solutions to implement a robust data strategy in their manufacturing processes.
Data Strategy for Manufacturing Processes
A data strategy in manufacturing processes is a structured plan that outlines how data will be collected, managed, analysed, and utilised to optimise operations and drive decision-making. Data Strategy involves establishing data governance frameworks, selecting data collection platforms, and integrating data from various sources, such as sensors, machines, and enterprise systems, into a single platform. A manufacturing data strategy guides efficient data collection, management, analysis, and utilisation, optimising operations and helping with informed decision-making. By utilising data strategically, manufacturers can gain valuable insights, identify opportunities for improvement, and stay competitive in today's rapidly evolving landscape.
Key components of a comprehensive data strategy for manufacturing include:
- Data Collection and Integration: Involves gathering data from various sources, including sensors, machines, and enterprise systems, and integrating it into a centralised platform for analysis and decision-making.
- Data Storage and Management: Encompasses selecting appropriate storage solutions and establishing robust data management practices to ensure data accessibility, reliability, and scalability while adhering to regulatory requirements.
- Data Analysis and Interpretation: Utilises advanced analytics techniques to derive actionable insights from collected data, enabling informed decision-making, process optimisation, and predictive analytics for future trends and patterns.
- Data Security and Compliance: Focuses on implementing measures to safeguard data integrity, confidentiality, and availability while ensuring compliance with industry regulations and standards to mitigate data breaches and non-compliance risks.
Why is it important to have a Data Strategy in Manufacturing?
Having a data strategy is crucial in manufacturing processes as it offers several benefits like:
- Data-Driven Decision-Making: A well-crafted data strategy ensures access to accurate and timely machine data, empowering decision-makers to optimise production schedules, inventory management, and resource allocation.
- Increased Operational Efficiency: Implementation of a data strategy streamlines operations, identifies improvement areas, and uses analytics to reduce bottlenecks, minimise downtime, and optimise workflows.
- Quality Assurance and Defect Prevention: Data analysis enables real-time monitoring of product quality, aiding in defect identification, waste reduction, and maintenance of high standards.
- Supply Chain Optimisation: A comprehensive strategy improves supply chain visibility, tracks inventory, evaluates supplier performance, forecasts demand, and optimises logistics for timely deliveries.
- Predictive Maintenance: Utilising data analytics for predictive maintenance anticipates equipment failures, reduces unplanned downtime, cuts maintenance costs, and prolongs equipment lifespan.
- Risk Management and Mitigation: Adherence to industry standards is critical in regulated sectors like pharmaceuticals and automotive. A sound data strategy ensures compliance, mitigates risks and avoids penalties through accurate record-keeping and documentation.
Challenges with Traditional Data Collection Methods
Traditional data collection methods pose several challenges in manufacturing:
- Manual Data Entry Errors: Relying on manual data entry leads to inaccuracies and errors, undermining data reliability and decision-making.
- Lacks Real-time Visibility: Traditional methods lack real-time insights into operational performance, hindering timely interventions and optimisations.
- Scalability and Efficiency Constraints: Traditional approaches struggle to scale with growing data volumes and fail to handle increasing complexity in manufacturing processes efficiently.
- Security and Data Integrity Risks: Security vulnerabilities and concerns over data integrity grow with traditional methods, leaving systems susceptible to data breaches.
What types of Machine Data should you collect?
- Machine data: Machine-generated information, including performance metrics, maintenance logs, and operating parameters.
- Order data: Details related to customer orders, such as order numbers, quantities, delivery dates, and specifications.
- Material data: It includes data related to characteristics and specifications of materials used in production, including inventory levels, suppliers, and quality attributes.
- Tool data: Information about tools and equipment utilised in manufacturing processes, including maintenance schedules, usage logs, and calibration records.
- Personnel data: Data about workforce management, including employee schedules, training records, certifications, and performance evaluations.
How can Data Collection Systems help manufacturers?
Manufacturers switch to data capture software for factors like efficiency, accuracy, and adaptability in modern manufacturing environments. With the rising complexity of operations and the growing volume of data generated, these software solutions provide a centralised platform for streamlined data management, ensuring consistency and reliability across various production stages.
- Improved Accuracy and Reliability: Data collection software enhances the accuracy and reliability of data, reducing errors associated with manual processes and ensuring data integrity throughout manufacturing operations.
- Real-time Data Insights and Decision-making: These software solutions provide real-time data insights, enabling manufacturers to make informed decisions swiftly, respond to changing market dynamics, and optimise operational performance efficiently.
- Scalability and Flexibility: Data capture software offers scalability and flexibility to accommodate the growing complexity and volume of manufacturing operations. This scalability enables manufacturers to adapt to evolving business needs and expand their operations seamlessly.
- Integration with IoT and Industry 4.0: Integration capabilities with IoT (Internet of Things) and Industry 4.0 initiatives allow manufacturers to harness the power of connected devices and smart technologies. This integration enables predictive maintenance, proactive decision-making, and optimisation of manufacturing processes for improved efficiency and productivity.
Steps for implementing a Data Strategy in your shop floor
By following these steps, you can systematically implement a data strategy on your shop floor, optimising operations and driving better decision-making.
Assess the Current State
- Conduct a thorough analysis of your shop floor processes and data systems
- Identify existing data sources and integration challenges.
Define your Objectives for Data Collection
- Clearly outline the business goals you need to achieve through data utilisation.
- Prioritise Key Performance Indicators (KPIs) for improved efficiency and productivity.
Select the right Data Collection and Analysis Tools
- Choose the suitable data collection system for your shop floor.
- Implement solutions that support real-time data collection and analysis.
Establish Data Governance
- Set up robust data governance policies to ensure data quality, security, and compliance.
- Define roles and responsibilities for data stewardship within your organisation.
Integrate the Systems
- Integrate systems on the shop floor to create a seamless data collection and management ecosystem.
- Implement IoT devices for real-time monitoring and data analysis for informed decision-making.
Focus on Continuous Improvement
- Implement a feedback loop for ongoing assessment and improvement.
- Regularly review and update your data strategy based on evolving business needs.
Application of data collection system in Manufacturing Operations
- Supply Chain: Data capture enables real-time tracking of inventory levels, shipment statuses, and supplier performance, enhancing transparency and optimising supply chain management processes.
- Demand Forecasts: Manufacturers can generate accurate demand forecasts, optimise inventory levels, and mitigate stock outs or overstock situations by capturing data on historical sales, market trends, and customer preferences.
- Maintenance: Data capture facilitates predictive maintenance by monitoring equipment performance metrics, identifying potential issues early, scheduling timely repairs, and minimising unplanned downtime.
- Production: Capturing production data allows for monitoring of throughput, cycle times, quality metrics, and process efficiencies, enabling continuous improvement initiatives and optimal resource utilisation. Tracking these production metrics is relevant for shop floor processes:
- Downtime: Inactive duration of production machinery/processes, impacting productivity.
- Changeovers: Time to transition equipment/processes between products, affecting efficiency.
- First Quality Pieces: Number of products meeting quality standards initially, reflecting operational effectiveness.
- Scrap: Defective materials/products, indicating inefficiencies.
- WIP Inventory: Partially completed products/materials in production, affecting resource allocation.
- Performance to Schedule: Comparison of actual production output to planned targets, measuring efficiency.
- Sales and Customer Satisfaction: Through data capture on sales transactions, customer interactions, and feedback, manufacturers can gain insights into customer preferences, identify trends, tailor products and services accordingly, and enhance overall customer satisfaction.
Implementing a robust data strategy is important for manufacturers seeking to thrive in an increasingly competitive landscape. The adoption of data collection software emerges as a solution, offering unparalleled accuracy, real-time insights, and scalability necessary to navigate complex manufacturing processes efficiently.
By harnessing the power of data collection software, manufacturers can improve operations, enhance decision-making capabilities, and pave the way for continuous improvement and innovation. Embracing technologies like automated data collection not only drives operational excellence but also positions manufacturers at the forefront of Industry 4.0 initiatives, empowering them to meet evolving customer demands and achieve sustainable growth in today's dynamic market environment.